厚鋼板焊接常見缺陷及預防
根據您提供的文本內容,厚鋼板焊接過程中的常見缺陷包括**氣孔、夾渣、未焊透和裂紋等**。為預防這些缺陷,可以采取以下措施:,,1. **表面清理**:在焊接前徹底清除鋼板表面的銹跡、油污及氧化皮,確保鋼板表面無雜物和凹凸不平。對于切邊鋼板,邊緣應處理平滑,無鋸齒形或深度不大于2mm的個別發紋。, ,2. **內部氣體處理**:檢查并處理板坯內部聚集的氣體,如皮下氣孔或氣泡,避免在焊接時氣體不能焊合造成的缺陷。,,3. **設計優化**:在鋼結構深化設計階段,通過節點設計減少焊接應力集中,避免或減少使母材板厚方向承受較大的焊接收縮應力。,,4. **坡度過渡處理**:在焊縫高出薄板厚度處,應將焊縫焊成斜坡狀,最大允許值為1:2.5;或在焊接前加工成斜坡,坡度最大允許值為1:2.5。,,5. **多層焊接連續性**:多層焊接時,應注意不連續,以避免冷裂紋的產生。,,6. **現場處理**:對超出規定厚度的鋼板進行特殊處理,比如在高出薄板厚度處進行斜坡焊接,以減少應力集中和未熔合等缺陷。,,7. **機械加工**:對于直接承受動載荷且需要進行疲勞驗算的結構,斜坡坡度不應大于1:4,以保證焊接接頭的穩定性。,,8. **熱切割與砂輪打磨**:當采用熱切割或機械加工無法實現平緩過渡時,可采用砂輪打磨的方法來達到所需的坡度要求。,,9. **焊接工藝選擇**:選擇合適的焊接方法,如手工電弧焊、氣體保護焊等,以適應不同材料和結構的要求。,,10. **焊接參數優化**:調整焊接電流、電壓、速度等參數,確保焊接過程穩定,避免因參數不當導致的缺陷。,,厚鋼板焊接中常見的缺陷及其預防措施主要包括氣孔、夾渣、未
厚鋼板焊接常見缺陷及預防
厚鋼板焊接過程中可能會遇到多種缺陷,這些缺陷可能會影響焊接質量,甚至導致結構安全隱患。以下是厚鋼板焊接的一些常見缺陷及其預防措施:
1. 未焊透
原因分析:未焊透通常是由于對口間隙過小、坡口角度偏小、鈍邊厚、焊接線能量小、焊接速度快、焊接操作手法不當等原因造成的。
預防措施:
- 嚴格執行標準要求,確保對口間隙不小于2㎜。
- 根據壁厚選擇合適的坡口類型,如壁厚小于20㎜的焊口采用V型坡口,單邊角度不小于30°;不小于20㎜的焊口采用雙V型或U型等綜合性坡口。
- 選擇合適的線能量、焊接速度和操作手法。
- 使用短弧焊接,以增加熔透能力。
2. 未熔合
原因分析:未熔合可能是由于固體金屬與填充金屬之間(焊道與母材之間),或者填充金屬之間(多道焊時的焊道之間或焊層之間)局部未完全熔化結合,或者在點焊(電阻焊)時母材與母材之間未完全熔合在一起。
預防措施:
- 適當加大焊接電流,提高焊接線能量。
- 焊接速度適當,不能過快。
- 熟練操作技能,保持正確的焊條(槍)角度。
3. 氣孔
原因分析:氣孔是在熔化焊接過程中,焊縫金屬內的氣體或外界侵入的氣體在熔池金屬冷卻凝固前未來得及逸出而殘留在焊縫金屬內部或表面形成的空穴或孔隙。
預防措施:
- 焊條進行烘培并裝在保溫筒內,隨用隨取。
- 焊絲清理干凈,無油污等雜質。
- 焊件周圍10~15㎜范圍內清理干凈,直至發出金屬光澤。
- 注意周圍焊接施工環境,搭設防風設施,管子焊接無穿堂風。
- 氬弧焊時,氬氣純度不低于99.95%,氬氣流量合適。
- 盡量采用短弧焊接,減少氣體進入熔池的機會。
- 合理操作手法,焊條、焊槍角度合適。
- 合適的焊接線能量,焊接速度不能過快。
- 按照工藝要求進行焊件預熱。
4. 夾渣與夾雜物
原因分析:夾渣與夾雜物是指熔化焊接時的冶金反應產物,例如非金屬雜質(氧化物、硫化物等)以及熔渣,由于焊接時未能逸出,或者多道焊接時清渣不干凈,以至殘留在焊縫金屬內。
預防措施:
- 焊件焊縫破口周圍10~15㎜表面范圍內打磨清理干凈,直至發出金屬光澤。
- 多層多道焊時,層間藥皮清理干凈。
- 焊條按照要求烘培,不使用偏芯、受潮等不合格焊條。
- 盡量使用短弧焊接,選擇合適的電流參數。
- 合適的焊接速度,不能過快。
5. 裂紋
原因分析:裂紋是焊接過程中或焊接完成后在焊接區域中出現的金屬局部破裂的表現。
預防措施:
- 控制焊接參數,避免焊接過程中產生過大的應力。
- 采用合理的焊接順序,減少焊接變形。
- 對于厚板焊接,應加強對層間溫度的控制,避免層間溫度過高或過低。
6. 焊接變形
原因分析:焊接變形是由于焊接過程中金屬的熱膨脹和收縮引起的。
預防措施:
- 在焊接之前,應根據鋼板的性質和厚度,確定合適的焊接參數,盡量控制焊接時間和溫度。
- 采用合理的焊接順序并選用合適的焊接規范和操作方法。
- 采用反變形和剛性固定措施。
通過以上措施,可以有效地預防厚鋼板焊接過程中可能出現的各種缺陷,確保焊接質量和結構安全。
厚鋼板焊接應力控制技巧
厚鋼板焊接變形矯正方法
厚鋼板焊接熱影響區處理
厚鋼板焊接質量檢測技術
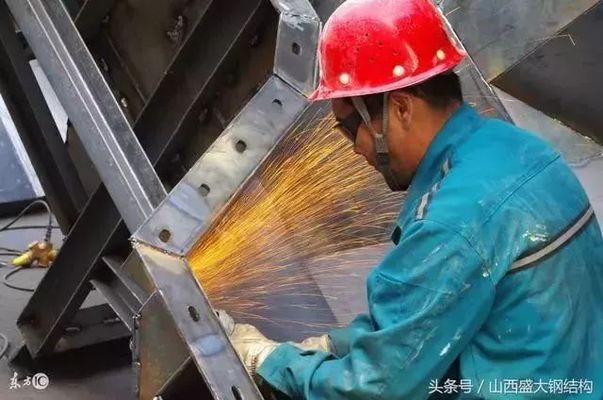
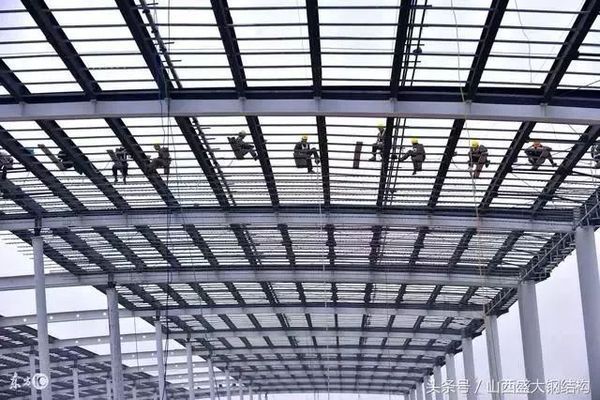
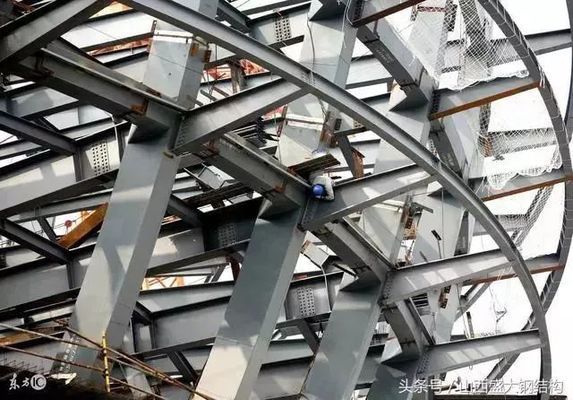
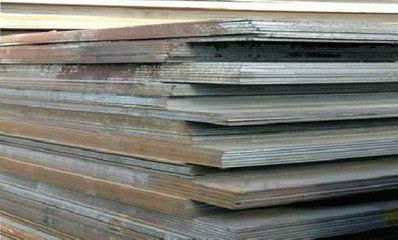
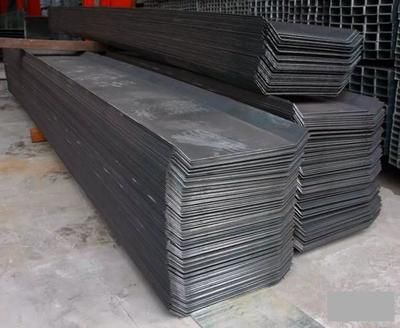
發表評論
還沒有評論,來說兩句吧...